‘핵융합硏 군산 플라즈마기술연구소’ 연구 현장 방문 취재
반도체 공정 진단 장비 국산화 위한 융합연구단 총괄 지휘
2026년까지 AI기반 플라즈마 공정장비 지능화 연구 완료 목표
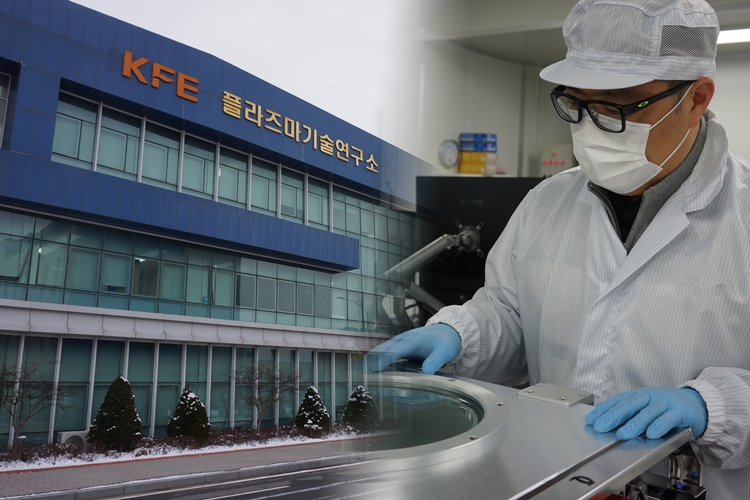
시사위크|군산=박설민 기자 한국 첨단 국내 정보통신기술(ICT)산업의 꽃은 단연 ‘반도체·디스플레이’다. 자동차부터 스마트폰, 인공지능(AI)에 이르기까지 대부분의 ICT산업군은 이 두 기술 분야에 의존한다. 관련 산업 수출액도 가장 많다. 과학기술정보통신부가 발표한 ‘11월 ICT 수출입 동향’에 따르면 반도체·디스플레이의 수출액은 총 116억4,000만달러. 전체 ICT수출액(178억8,000만달러)의 약 65%를 차지한다.
하지만 국내 반도체·디스플레이 산업은 외산 장비와 기술이라는 사상(沙上)에 쌓인 누각(樓閣)이다. 삼성전자와 SK하이닉스, 삼성·LG디스플레이 등 국내 핵심 기업들 모두 외산 장비에 의존하고 있다. 세계 최고의 반도체 강국이라는 한국이 매번 ‘슈퍼 을(乙)’이라 불리는 네덜란드의 ‘ASML’과 미국의 ‘램리서치’에 쩔쩔매는 것도 이 때문이다.
산업계 관계자 및 전문가들은 한국 반도체·디스플레이 산업이 경쟁국과의 격차를 벌리기 위해선 결국 ‘공정 장비 국산화’가 필수라고 강조한다. 이에 <시사위크>에서는 ‘플라즈마장비지능화연구단’의 연구 현장을 방문, 우리나라 반도체·디스플레이 공정 진단 신기술 연구 현황을 살펴봤다.
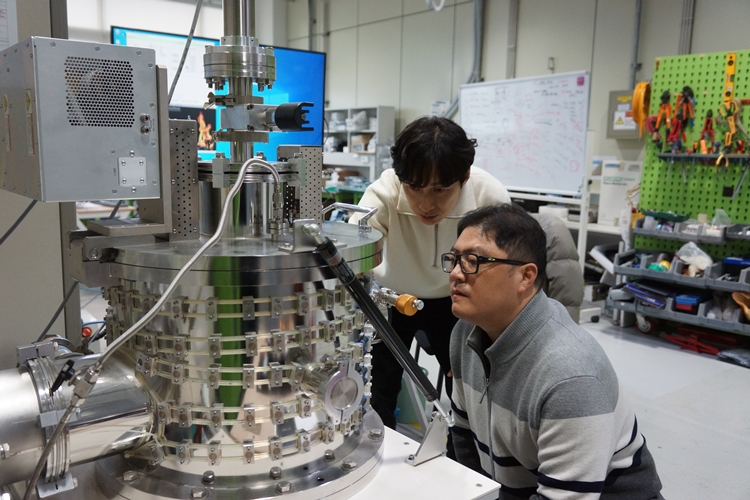
◇ 반도체 공정 국산화 위한 연구단의 ‘심장’… 2026년까지 기술 완성 목표
19일 오전 10시. 차가운 바닷바람을 뚫고 전라북도 군산항 인근에 위치한 국가 연구소에 도착했다. 관계자들의 안내에 따라 들어선 연구소 내부는 눈 뜰 새 없이 바쁜 모습이었다. 서류 뭉치를 들고 연구소 내를 바쁘게 돌아다니는 연구원들의 모습은 공상과학영화 속 과학자들의 모습을 연상케 했다.
기자가 방문한 이 연구소의 이름은 ‘한국핵융합에너지연구원(핵융합연) 군산 플라즈마기술연구소’. 국내 유일 정부출연 ‘플라즈마’ 기술 전문연구기관이다. 플라즈마란 기체가 초고온 상태로 가열돼 전자와 양전하 이온으로 분리된 것이다. 고체, 액체, 기체 다음의 ‘물질 제 4의 상태’라고도 불린다. 반도체, 조명, 디스플레이, 의료장비, 태양전지 및 신에너지 개발 등 다양한 첨단기술연구에 융복합적으로 적용된다.
현재 군산 플라즈마기술연구소에서 중점적으로 진행하고 있는 연구 분야는 ‘플라즈마 공정 진단’이다. 지난 2020년 설립된 ‘플라즈마장비지능화연구단장’의 총괄 주관 연구수행기관이기도 하다. 이 연구단은 ‘한국과학기술연구원(KIST)’, ‘한국과학기술정보연구원(KISTI)’ 등 4개 출연연과 주요 7개 대학이 참여하고 있다. 2026년까지 총 440억원의 연구비를 투입, 반도체 플라즈마 공정장비 지능화 기술 개발 및 실증을 달성한다는 목표다.
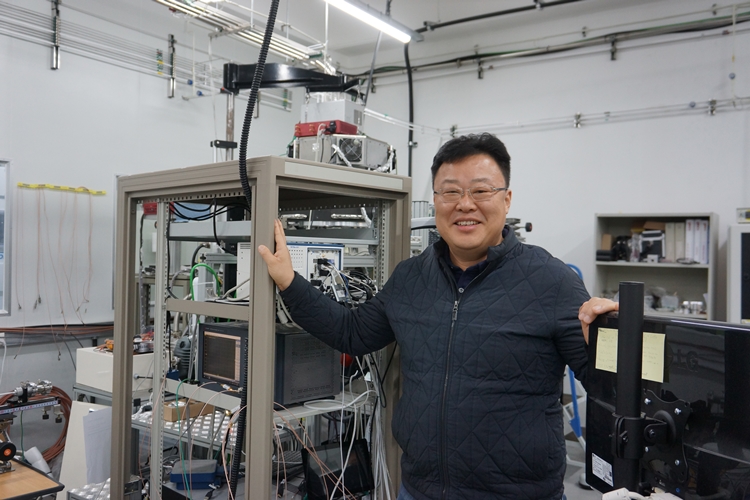
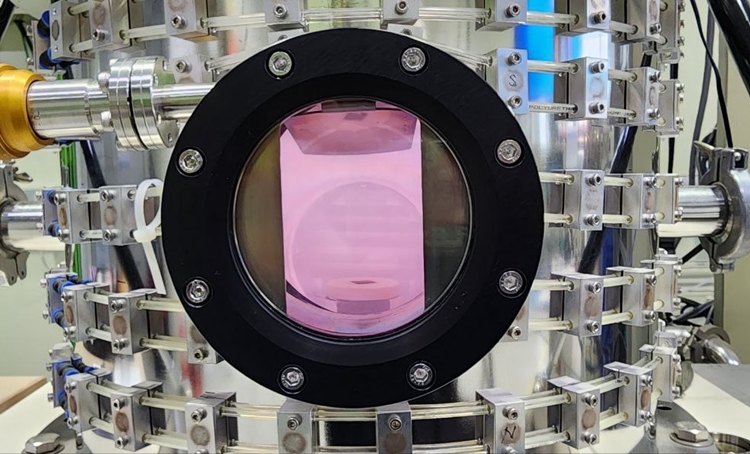
‘플라즈마 공정’은 반도체 제조용 가스를 통제하기 쉬운 플라즈마 상태로 만들고 이를 원자 단위로 조절하는 기술이다. 매우 정교한 회로를 만들 수 있어 반도체·디스플레이 공정의 꽃으로 불린다. 하지만 원자 단위의 오류를 찾아내는 것은 여간 어려운 일이 아니다. 이를 빠르고 정확하게 해낼 수 있는 반도체 공정 진단 장비 기술을 만드는 것이 이곳 연구단의 역할이다.
특히 ‘인공지능(AI)’ 기술을 활용한 반도체 공정 진단 기술은 연구단 사업의 핵심 과제라고 볼 수 있다. 연구단이 개발 중인 대표 기술 중 하나는 ‘AI-OES 센서’다. 반도체·디스플레이 공정 기기 내 플라즈마 변화를 AI로 모니터링하는 시스템이다. 먼저 센서로 공정 기기 내 상황을 실시간 관측한다. 그 다음 AI가 보정해 출력한 가장 정확한 예측 데이터 값을 엔지니어에게 전달한다. 복잡해보이지만 기술 원리는 혈압측정용 스마트 워치와 유사하다고 볼 수 있다.
윤정식 플라즈마장비지능화연구단장은 “현재 국내 대다수 반도체·디스플레이 기업은 공정 진단 기술에 국산 장비보단 외산 장비에 의존하고 있다”며 “군산 플라즈마기술연구소에서는 반도체·디스플레이 공정 장비의 국산화와 기술력 증진을 위한 지능화를 2026년까지 마치는 것을 목표로 연구하고 있다”고 말했다.
이어 “올해 10월 달까지 해서 3년 연구의 1단계가 끝난 상황으로 실험실 수준에서 할 수 있는 연구는 마무리됐다”며 “이제 실제 기술 실증인 2단계 사업을 진행할 예정으로 기업체 장비에 저희가 개발한 기술들을 가지고 같이 공동 연구를 진행할 계획”이라고 설명했다.
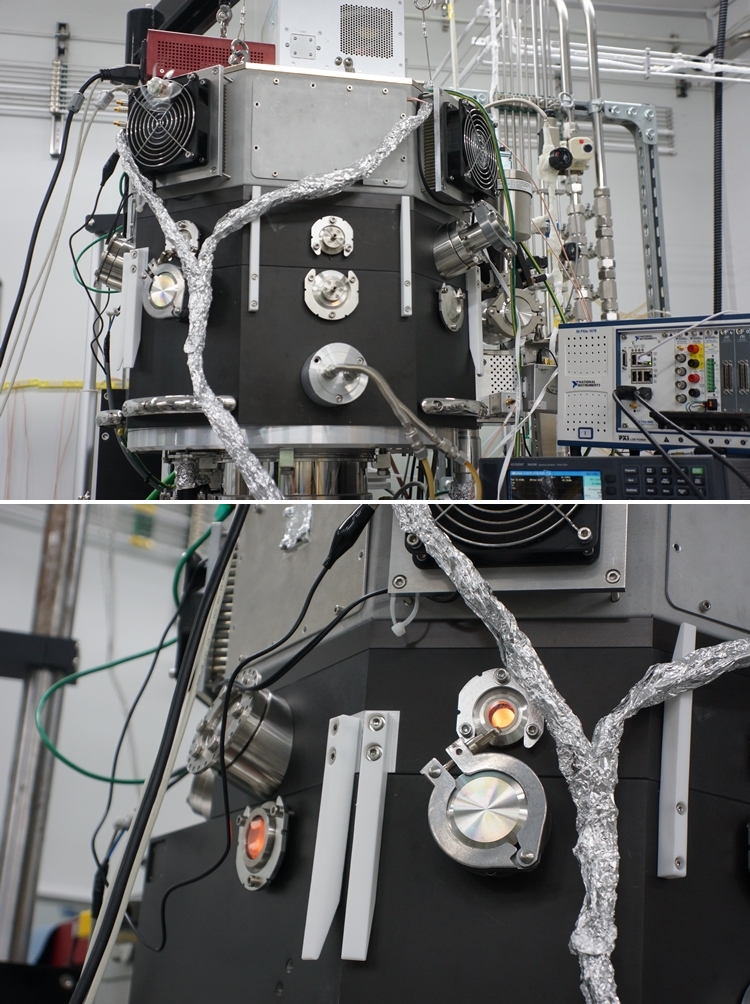
◇ 여러 종류의 플라즈마 공정 연구 진행… 수집된 데이터로 ‘공정진단 AI’ 학습
김종식 플라즈마장비지능화연구단 데이터연구팀 팀장의 안내에 따라 실제 실험 과정을 살펴보기 위해 실험실로 이동했다. 두꺼운 철문을 열고 들어선 실험실 내부는 상상하던 번쩍이는 ‘깔끔한’ 연구실과는 분위기가 사뭇 달랐다. 전자파 노이즈를 막기 위한 은박지로 둘러싼 전선들은 정글은 넝쿨처럼 여기저기 얽혀 있었다. 건조한 공기와 웅웅거리는 소음도 코와 귀를 자극했다.
실험실에 들어서자 가장 먼저 눈에 띈 것은 은색 물탱크처럼 보이는 장치였다. D램, 낸드 생산 공정에 사용되는 ‘산화막 식각 공정장비’였다. 이 장치는 주로 ‘고 종횡비 컨텍(HARC) 공정’에 사용된다. HARC는 층층이 쌓은 메모리 반도체에 매우 미세한 구멍을 깎아내는 플라즈마 식각 공정이다. 보통 100나노미터(㎚, 머리카락 굵기의 100분의 1수준) 단위로 공정이 이뤄지기 때문에 정확한 공정 진단은 필수다.
산화막 식각 공정장비에 가까이 다가서자 진공 챔버의 유리창 뒤로 주황색 빛이 붉게 빛나는 것을 볼 수 있었다. 김종식 팀장의 설명에 따르면 챔버 내부는 질소가스를 분해해 플라즈마화 시킨 상태였다. 연구팀은 이를 통해 질화 공정(Plasma nitridation) 공정 및 플라즈마 특성을 관찰한다.
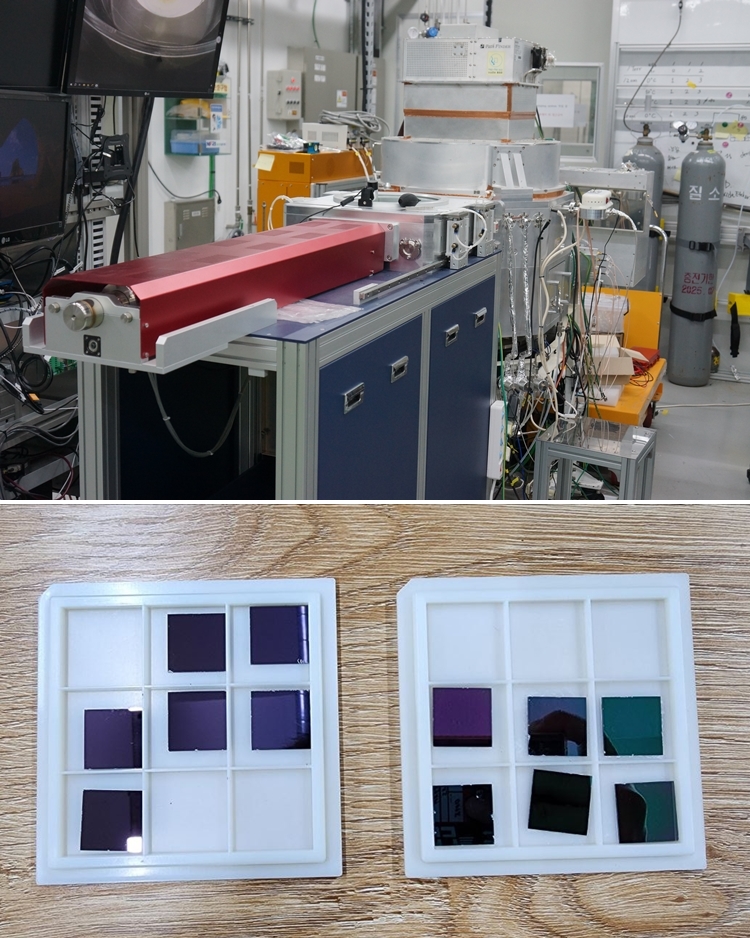
산화막 식각 공정장비에서 공정을 마치고 밖으로 나온 반도체 패널은 기존의 푸른빛을 띈 보라색에서 청록색 빛으로 바뀌어 있었다. 김종식 팀장은 “웨이퍼 색의 변화는 실리콘 산화막 두께 차이에 따라 발생한다”며 “이 샘플의 경우 반도체·디스플레이 공정에서 주로 사용되는 불화탄소(CF)계열 가스로 실리콘 산화막을 식각했기 때문에 두께가 변화하면서 색이 변한 것”이라고 설명했다.
김종식 팀장은 “이곳에서는 질소가스로 플라즈마 발생을 시킨 후 발생하는 모든 현상을 관찰한다”며 “약 9개 이상의 진단장치가 돌아가며 내부 챔버의 플라즈마 상태를 분석하고 데이터셋으로 저장한다”고 말했다. 이어 “이렇게 수집한 데이터를 기반으로 연구원들은 시뮬레이션 및 AI 알고리즘 개발·학습을 진행한다”며 “이 기술을 다시 연구원들이 피드백해 실제 산업 현장에 어떻게 적용할 수 있을지 연구하고 있다”고 설명했다

◇ ‘청결부터 안전까지’… 철저한 안전 연구 현장 유지
개발된 AI시뮬레이션은 실제 반도체 공정기기에서 어떤 방식으로 테스트가 이뤄질까. 이를 확인하고자 테스트룸 내부도 취재를 진행했다. 관련 실험은 클린룸에서 이뤄졌다. 작은 먼지라도 들어갈 시 오류가 발생할 수 있어 청결 유지가 필요하기 때문이다.
철저한 청결 유지가 필수인 만큼 내부로 들어가는 과정도 복잡했다. 먼저 먼지 등 미세한 입자들이 신체와 옷에 달라붙지 않도록 하는 방진복과 방진화를 착용했다. 그 다음 에어샤워룸으로 들어가 약 15초 간 강력한 바람으로 남은 먼지를 모두 털어내는 과정을 거쳤다. 바람은 쓰고 있던 안경이 흔들릴 정도로 강력했다.
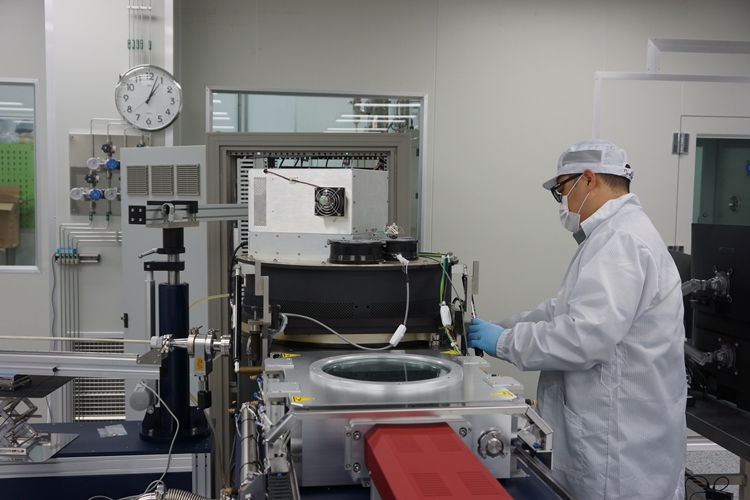
복잡한 절차를 거치고 들어간 클린룸 내부에서는 이미 연구진들의 실험이 한창 진행되고 있었다. 질화 공정장치에서 D램 반도체의 ‘게이트(Gate) 박막’을 성장시키는 실험이었다. 레코드판처럼 보이는 둥근 12인치 (300mm) 반도체 웨이퍼를 플라즈마 상태의 진공 챔버 내부에 집어넣으면 그 위에 실리콘 입자들이 달라붙는 방식으로 게이트 박막이 만들어진다. 이렇게 웨이퍼 위에 만들어진 게이트 박막은 반도체 전류 흐름을 조절하는 역할을 한다.
연구소는 실제 반도체 공정 생산 시설과 유사한 구조로 이뤄졌다. 때문에 내부 안전 관리도 철저히 이뤄지고 있었다. 위험하거나 환경오염을 일으킬 수 있는 공정 가스는 내부 장치를 통해 정화돼 밖으로 배출된다. 이 장치를 ‘스크러버’라고 부른다. 2021년 이후 실제 반도체 공정 회사들에서도 스크러버 장치 사용량을 대폭 증가시킨 것으로 알려졌다.
김종식 팀장은 “스크러버에는 여러 가지 타입이 있는데 현재 연구소에서 사용하고 있는 것은 플라즈마 상태로 바꿨던 공정 가스를 태워 안전한 물질로 바꿔준다”며 “CF계열 가스나 암모니아 가스 등을 거의 유해성이 없는 물질로 바꿔 안전하게 방출하기 때문에 공정상 환경오염은 거의 발생하지 않는다”고 말했다.